The Inpeco way to your tailor-made solution
Developing a lab automation layout is a long process, involving many different resources; MG. Pirozzolo offers an insight into this process
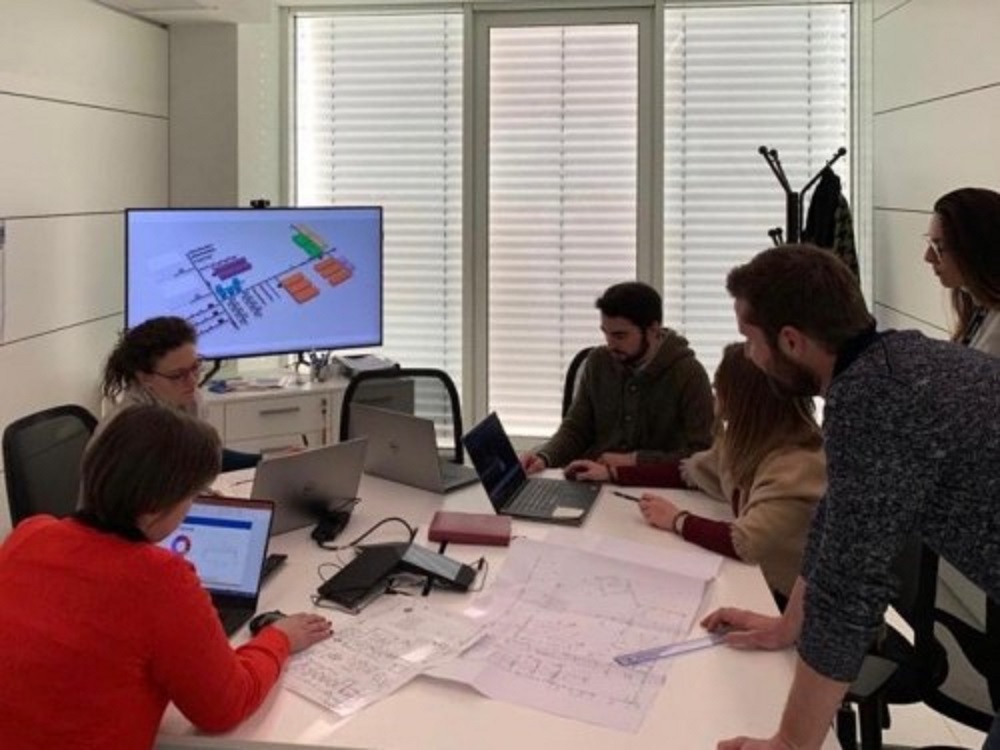
At Inpeco, we love to design and develop Total Laboratory Automation solutions. It is more than a job; it is a passion that drives us to fulfill our customers’ needs to the best of our abilities. Meeting demanding laboratory requirements is very hard work. Maria Grazia Pirozzolo, Inpeco’s Customer Solutions Manager, is in charge of a team of seven specialists with one mission: designing game-changing laboratory automation solutions.
1. Maria Grazia, could you tell us something about yourself, your professional background and the role of your team at Inpeco?
I’m a Biomedical Engineer and I started working for Inpeco as a Verification & Validation Engineer in 2005, soon after I graduated from the Politecnico di Milano. At that time, I dealt with new product releases, writing new module requirements and testing them through to the final launch. Later I became a Service Application Specialist, traveling worldwide to install Inpeco automation systems and train lab staff on their first experience with our products. I held this role for several years and eventually helped to coordinate the Application Specialists Team. At that time, I was often asked to collaborate on the development of automation projects for potential customers, and little by little I moved completely into a Pre-Sales role.
Since 2017, I head a team devoted to designing customized automation solutions for clinical labs. We are the Customer Solutions Specialists (CSS) Team within Inpeco’s Global Business Development Organization. The CSS Team comprises seven very “special” specialists, with design and engineering backgrounds, who process on average about 55 layouts per month. During my fifteen years with Inpeco, the interaction with customers and business partners has become increasingly constructive and now plays a central role both for my own and my team’s personal and professional growth.
2. Can you describe the process of developing an automation solution?
Our involvement differs considerably from case to case. There are projects where my team starts to study a solution from the very beginning, mapping customer needs, current workflows, and future requirements. These projects usually result in the design of the biggest, most complicated solutions. On the other hand, there are projects where our involvement is requested only during the final stage of reviewing and approving layouts proposed by local partner organizations.
Whether developing or reviewing a layout, the CSS Team has to collaborate with our sales colleagues on the field, with our local and global partner organizations, and with the end customer. Often, we also need to work with R&D, to understand possible new developments required to satisfy our customers’ needs. Sometimes our team’s involvement is requested so as to solve any possible installation criticalities in advance, during the layout design stage. Then, for every project that reaches the production phase, my team’s layout designers collaborate with the Manufacturing Technical Department to release the final configuration that is to be built and shipped. Another important task is the ongoing sharing of knowledge with our partners. The CSS Team, together with the Partner Solutions Specialists Team (PSS), regularly reviews and releases technical material and guidelines so that partner organizations can propose Inpeco solutions independently. We organize training sessions, both online and in-house, to keep our partner organizations up-to-date. During 2019, in addition to online sessions, we organized five in-house training courses attended by participants from around the world. This is always a great opportunity to share our mutual experiences.
3. What’s the biggest challenge when developing a layout?
Developing a layout is a long process that involves many different resources and can take up to several months. Many different aspects need to be considered: the customer’s needs, the workflow required, the lab’s technical equipment, the specific business scenario (a public tender, for example, involves different processes compared to a private procedure).
Sometimes, the information required to develop a new layout is difficult to obtain. And often, the final proposal needs to be ready in a very short timeframe. Also, the limitations, in terms of space and compliance with rules, change from country to country and from lab to lab. Meeting the customer’s desiderata, including the deadline, while also observing our solution specifications and development times, can be very challenging. But it is all part of the job, and we love it!
4. How do you think labs will change in ten years’ time?
It’s not easy to predict how labs will change in ten years’ time… but I believe the need for fully automated, controlled, traceable and patient-focused processes will no longer only be required by large, prestigious organizations; such processes are becoming a must for all laboratories, no matter how small or specialized. This means that, in terms of software and hardware specifications, our solutions need to become even more flexible and smarter than they are today: for example, solutions for scenarios in which decentralized and specialized labs need to be connected with state-of-the-art networks capable of managing the full patient process; or solutions that challenge mega and giga organizations, so that all lab specialties can move towards total laboratory automation.
5. What do you like most about your job at Inpeco?
I like to feel that Inpeco’s mission is my mission, and I love to work with people passionate about that mission. When the wind changes rapidly and the sea gets rougher, and the crew joins forces and keeps the boat afloat, navigating faster and better than before, you can’t help but be proud to be a part of that crew!